Made in paradise
Introduced in 14th-century Kashmir and popularised during the Mughal period, the Sozani craft is a fine needlework that has now emerged as an important source of livelihood in the valley
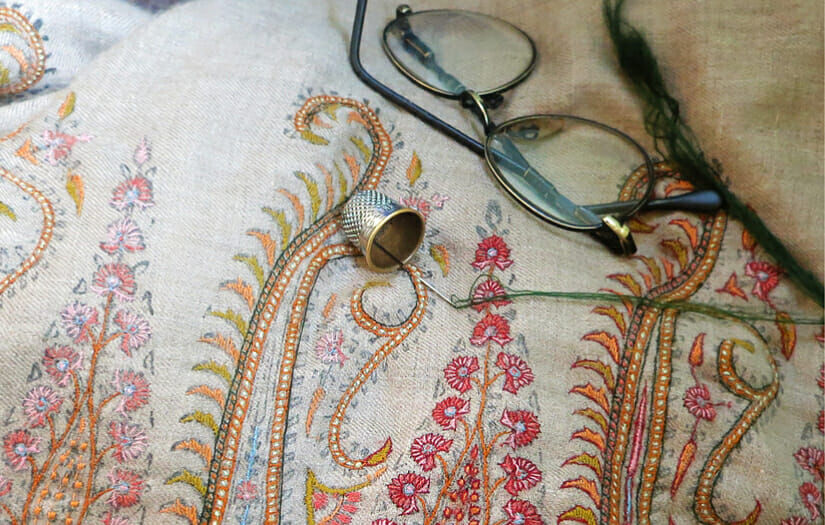
In describing Kashmir as a paradise on the Earth, Amir Khusro wrote, 'Agar firdous baroye zameen ast, hami asto, hami asto hami ast', meaning 'if there is a paradise upon earth, it is here, it is here, it is here'. It is in this paradise that the art of Sozni, an extremely fine, delicate and artistic needle work was introduced in the 14th century by Mir Syed Ali Hamadani, who moved with his followers and adherents to the beautiful vale to escape the persecution of the then tyrannical rulers in Central Asia.
According to some, the word 'Sozani' in Persian means needle; sozankari is needlework, and the practitioner of the craft is called the sozankar. However, another interpretation is that in the ancient Kashmiri lexicon, sozan meant a wise man. A contemporary mystic poet Sheikh-ul-Allam wrote, 'Sozan Ishara seeten bozan Kozan bozan na dum duma gath', meaning 'the wise will understand by small hints, whereas fools will not understand even if we cry aloud'. If the Kashmiri word sozan is taken as the etymological root of the Sozani then it means a craft performed by the wise men.
Be that as it may, it has become synonymous with the craft form in which embroidery is performed by the skilled traditional Sozani embroiderers of Kashmir, using motifs depicting geography of the land through coloured threads and fine needlework. The very fine Sozani work uses the Sozani stitch for outlining of the motif with a darker shade of thread while the filling up is done with the same fine Sozani stitches but in a different colour. There is no visible gap between the outline and the filling. The motifs are also outlined several times in different shades of colour. The empty spaces outside the motif are rendered with fine stitches of yet another colour. It appears very compact and expensive, and is therefore used on high value products like silks, pure Pashmina wool and crepes.
There are also two conflicting versions on how the craft came to be such an important source of livelihood. According to the first version, Syed Hamdani was accompanied by many Sayyads, Sufis, mystics and several hundred disciples. These people were also master craftsmen, embroidery specialists and artisans. As Hamdani rejected all forms of charity available for the Muslim religious class, it was incumbent upon each of them to earn their livelihood through work, as great emphasis was placed on Akl-i-Halal (earning the livelihood through legitimate sources of income). Hamdani was himself a Sozani master and designer. It is said that 'Hashiya' (the border) in Sozani on Kashmiri shawls is his invention
The second version is that as men and women from Kashmir's villages are mostly seasonal farmers involved in fruit and cereal farming, many of these farmers turn into artists when they are not busy with farming. Sozankari was thus an additional source of livelihood for the Kashmiri farmer.
The art form received a further boost during the reigns of Sultan Sikander and Badshah Zainul Abideen (1380-1420 CE). According to Abul Fazl, a chronicler of Mughal times, this was the period when Iranian culture became the order of the day and Kashmir was called Iran-I-Saghir (Minor Iran). The Mughal nobility too extended their patronage to this craft. Sozani now appeared on their robes, gowns and sashes, with embroidery using golden and silver threads. Akbar's admiration for embroidered shawl designs is well documented, and he invited designers from Persia to improve the embroidery and shawl designs. Persian merchants and traders took the Sozani embroidered sashes to the salons of Europe where they became a style statement.
We will now discuss the five stages of the Sozani embroidery process. These include design, carving, embroidery, imprinting, and finishing. In the first instance, the design is made by a Naqash (Designer) on a tracing paper. The designs are created by a senior embroidery Kaarigar (craftsman). It is then carved into wooden blocks which can be used to create imprints on the fabric. The blocks are filled with either charcoal paste or chalk paste to impart black or white colour to the imprinted design. Once the design is imprinted on the fabric, the embroiderer uses a fine needle and thread to make the embroidery. The thread is usually of silk or a high quality cotton. The last stage is finishing. Once the embroidery is done, the shawl goes through the cleaning and final finishing process.
The GI for this commodity was applied for, and obtained by the Craft Development Institute of Srinagar, and includes all those associated with the craft of 'fine needlework on various fabrics', done by a Sozankar employing predominantly the Sozani stitch, Darn stitch, Buttonhole stitch, Herringbone stitch, Chain stitch, Satin stitch, Knot stitch and Stem Stitch using silk and viscose yarns.
Sozani is growing from strength to strength, and adding to the prosperity of the Vale!
Views expressed are personal