Cast to perfection
Boasting of deep civilisational roots, the uniquely casted Bastar bell metal craft — as an earthbound expression of nature and folk life — has gone on to consolidate an impressive market for itself
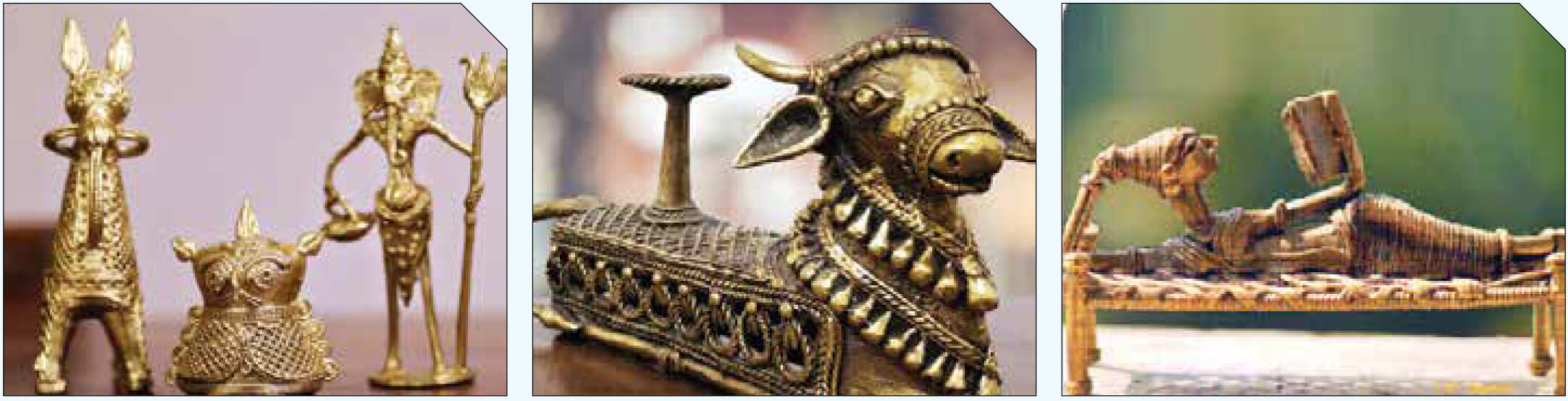
The first evidence of the Dhokra (bell metal) craft was discovered in the relics of Mohenjo-Daro and Harappa civilisations, which suggests the historical and traditional importance of the industry. The iconic statue of the dancing girl, unearthed at Mohenjo-Daro, is the proof of origin, salience and continuity of the craft.
As academician Rajesh Kochhar points out in his monograph, 'Dhokra: The Traditional Art of Metal Casting', "if Mohenjo-Daro craftsman who famously cast the bronze figurine of a dancing girl some 4,500 years ago were to visit central and east India today, he would undoubtedly feel at home. In the Dhokra metal-casting process, he will recognise the lost wax technique". It is this unbroken tradition, coupled with the intrinsic starkness and vitality of the art form, which makes Dhokra a coveted collector's item in India and abroad for connoisseurs, scholars and laypersons alike.
Today, Dhokra art is a major attraction of Bastar. As the craftsmen are mostly from the Ghadawa community, it is also known as the Ghadawa art. The name Ghadwa is derived from the word 'Ghalna' which means to melt, and as these people prepare the craft items by melting the metal using a lost wax technique, they are given the name 'Ghadwa' which means the act of shaping and creating. In some regions the craftsmen are also called 'Ghasia','Khaser', 'Mangan' and 'Vishwakarma'.
The legendary Dhokra shilp guru Jaidev Bhagel describes the origin of the Dhokra craft as follows: An ancient 'Adivasi' hunter, unable to find anything nearby, strayed far into the thickly forested area. In the deep forest, it was arid and dry. Exhausted he felt asleep. A forest fire woke him and on way home he spotted a shiny metal piece in a form as if it had been poured from the stone above. On subsequent visits and observation, the mystery was solved. An insect had hollowed a stone (or used stone with hole perhaps) and made waxen hive for home inside and the hollow of the stone. With the forest fire, the metal ore within the stone had melted and dropped down; upon solidifying it bored the impression of the waxen hive. This is how Bastar Dhokra work came into being.
The process of making the moulds is as old as the craft. All the decoration is done on the dyes with wax strings. Wax is the appropriate medium for this craft because of its unique softness and malleability. It can be drawn out in wires of required diameters and can be moulded into desired shapes. The people there worship the sun, moon, fields, mountain, jungle, etc., which form a major part of their designs and motifs. They make idols of deities, and puja accessories like bells, oil lamps, incense stick holders, etc. The craft has its very foundation rooted in the religious beliefs and practices of the people.
This ancient tradition received a fillip in the 1960s when the Bangla refugees from the erstwhile East Pakistan (now Bangladesh) were resettled in the Dandakaranya region. Administrators from the ICS and IAS looked upon this craft as a source of livelihood — not just for the tribals, but also for the settlers. This is how the craft found a 'market', and state emporia encouraged journalists and media people to visit Bastar, document the tradition and write about it. Thanks also to the organisations like the Crafts Corporation of India, that artists like Jaidev Baghel, a bell metal artisan from Kondagaon, achieved international popularity on account of participation in festivals and various shows. This led the private sector exporters to invest in the production and marketing of the craft.
We now come to the method of production. The raw materials include black soil (chikti mitti), a soil of volcanic origin which contains clay; and rice husk (bhoosa) which is mixed with the soil to hold it together, as clay tends to break apart easily when dry. This also makes the mould porous, and prevents the cracking of the mould during firing. The next ingredient is riverside soil (rui mitti). This is the soft soil procured from the river beds, and is easy to shape, mould and file. The red soil is mixed with cow dung (gobar) as it allows the wax to melt out of the cast and not get stuck on to the soil. But the critical element is red soil (lal mitti) which is formed by the ant homes in the soil. The soil is picked up as it is. Dhokra also involves the use of bean leaves (sem patta) which is chosen because of its high-water content. Finally, there is bee-wax (madhumakkhi ka mome) which is extracted directly from the bee hives. These days, paraffin wax (mombatti ka mome) is also used, though it has to be mixed with damar (coal tar) and agarbatti dhoop to prevent it from cracking.
The castings are done in bell metal – a mixture of two alloys, brass and bronze. Brass adds shine to the surface while bronze adds glitter. Brass being more viscous does not easily flow into the casts; bronze being heavy and less viscous helps in the molten mixture to flow easily and through narrow channels. Last but not the least, there is the firewood (jalawan) obtained from the forest, and wood coal (koyla) which is used to prepare mixture for covering layer on model.
The metal images of Bastar are peerless not only for the technique of casting, but also for their earthbound expression of life and celebration. Abundance of nature and folk, along with cultural traditions, together form the unique inherent basic fabric of tribal heritage of Bastar. The GI is held by the Chhattisgarh Hastshilp Vikas Parishad which is also engaged in the promotion, production and market linkages of the product.
Views expressed are personal