An alluring ornament of Firozabad
Firozabad bangles are one among the wide spectrum of centuries-old traditional glassware products of the region, which are realigning themselves with contemporary, eco-friendly designs and packaging
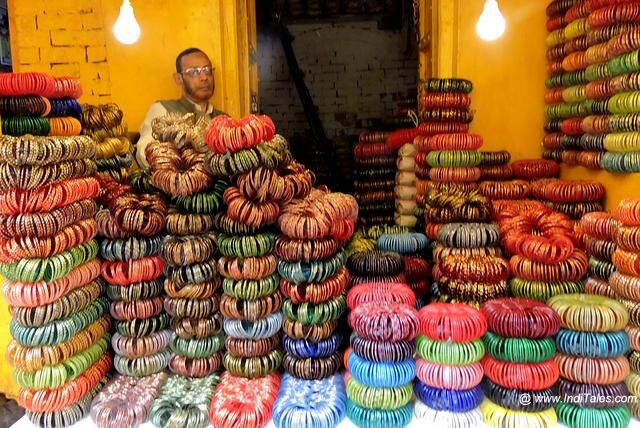
With an annual turnover of nearly 10,000 crores and employment to nearly six lakh workers – mostly in the informal sector — the glass industry of Firozabad in UP, about forty kilometres from Agra, is coming to terms with the regulatory frameworks on environment and labour standards. The Supreme Court has given directions with regard to furnaces: as such, natural gas is now used as a fuel in place of conventional fossil fuels and the standard height of a furnace chimney is now at least 60 feet. Secondly, and perhaps even more importantly, civil society organizations and the education department of UP have supported initiatives to ensure effective implementation of the Right to Education Act. However, it must be placed on record that till a few years ago, child labour and unhygienic and unhealthy working conditions were the defining features of this industry. Even though there are gaps in compliance, the positive signs need to be acknowledged and supported.
As such, this column begins by lauding the efforts of Disha Children's Programme in establishing Child Protection Committees in every slum, comprising children, ward officers, parents of children, Anganwadi, primary school teachers and ASHA workers. The children edit and print a bi-annual publication 'Balvani-Bacchon ki Awaz' which, while showcasing the creative output of children, has also focused on improving the school infrastructure, especially with regard to toilets and drinking water. It also supported the campaign against child marriage.
Let us now discuss the tradition of glassware and bangle-making in this region. This was part of Hastinapur from where glass beads and bangles dating 1100-800 BCE were reported by researchers DP Agarwal and Manikant Shah in a 1985 publication of the Indian National Science Academy. We are also aware that during the Yajur Veda period, ornaments for women were made of glassware. Alan Macfarlane and Gerry Martin draw upon references in Ain-i-Akbari in their monograph 'Glass in India' (2002) to confirm that during the Mughal period, glass articles, like chandeliers, tumbler, bowls and bottles for perfumes were manufactured in Firozabad — a town which was named after Akbar's powerful Mansabdar Firoz Shahin 1566. It is said that prior to this, the name of the locality was Chandwar Nagar. Another name for this town is Suhag Nagari on account of its connection with bangles and their association with married women.
The product spectrum of Firozabad glassware is very wide. It can be divided into the following four classes on the basis of the technology applied in their manufacture: (a) glass bangles (choori) craft; (b) glass beads craft; (c) products manufactured using mouth/lungs blowing technique; and (d) products manufactured using machinery. We shall focus on bangles, whose manufacture and finishing are a 'world unto itself'. It is said that a bangle passes through 54 expert hands of artisans before getting ready to be admired by ladies.
Bangle-making can be divided into three main parts: the first of which involves the rolling of glass layer on wooden rods, which would be cut into the shape of bangles (choori). The next steps are: aligning (sidhai), joining (judai), grooving the designs on the upper side of the bangles and baking the bangles in muffle furnace (pakki bhatti) to make them smooth and bright. Finally, the task of decoration with jari, ceramic work or silver or golden colouring is done.
The colouring of bangles is done by either using coloured glass or applying colours to the top/upper crest of the bangle. There are different methods for using colour in the glass. A colour layer (batti) is sandwiched between two transparent glass layers at the time of making gulli. Melted glass taken from the furnace is unrolled/spread upon a flat metal sheet and then it is re-rolled upon an edge/side of a stick. Then it is given a shape by pressing it accordingly. The bangle could be round, flat, oval or spiral on the basis of beating the loam in a particular fashion.
The gulli is put into another furnace in which melted glass wire from the gulli is thrown to the rotating round-shape rod (baelan). The radius of the rod decides the radius of the bangles manufactured. Once a wire from gulli gets rolled on the rotating rod (baelan), it keeps rolling on the rod just like glass wire getting rolled on the rod, creating a spiral shape ring of glass. A rod full with the rolled glass thread is known as muttha. Two artisans sit on the opposite sides of the furnace. At one side the first artisan, known as tarkash, puts the gulli inside the hole of the furnace and does the process of getting struck glass wire from gulli to the rotating rod (baelan). Before the first gulli exhausts, the next gulli is attached and the process continues!
The geographical indicator for bangles, as well as for manufacture of kitchenware, tableware, chandeliers, double-walled glass refills, glass bangles, beads, tumblers and decorative items is held by the Glass Industry Syndicate — the oldest surviving glassware industry association in Firozabad. Established in January 1946 with 70 members, it is now the trade promotion body for 421 glassware units at Firozabad, who are now keen to transform the industry to make the products eco-friendly with an element of contemporary design and packaging.
Views expressed are personal